GIMP redux, enter: the schmuck
20 May 2009, 09:56
‘What about schmuck?’ Katrin Alt said, when I explained to her about my work on GIMP. —Excuse me? ‘You know, what about CMYK.’ —Ah, that is a long story.
So started my talk at the libre graphics meeting this year. I will cover it in three separate blog entries, the first one being about schmuck.
hot debate
GIMP’s lack of CMYK mode is one of the hottest topics in the comments sections out there. Also fiery is the resistance by GIMP’s maintainers to introduce such a mode. In March the CMYK issue returned during a long thread on the GIMP developer mailing list. Quite a few users who seriously use and need color separations chipped in. It gave me a chance to understand the activity, both from a technological and users’ side.
The first thing to understand about the CMYK issue is that it is not about CMYK. The issue is bringing artwork to printing presses. And I mean serious printing presses, with operators, print runs and hydraulic parts. Not that very expensive, high‑spec printer that sits in the corner of the designer’s office, that one is still covered by openPrinting.
flex plate
Unlike for the printers that you and I use, with printing presses the plates that do the printing are freely configurable. Any number of plates can be used with literally any kind of ink/paint/lacquer, for cost or quality reasons. That there is a world beyond CMYK is something that Øyvind Kolås has been pressing on me, for instance, during a discussion last year at guadec.
During the mailing list discussion mentioned above, Louis Desjardins wrote to have a look at packaging for examples of how complex the plate set‑up can get. So I did, the next time I made a coffee. Turning over the milk carton, I found the marks for a seven‐plate print job, none of which was cyan, magenta, yellow or black.
mind the gap
Now, I am not saying that GIMP is the application for designing milk cartons, but the complexity of printing such a cheap commodity really shows that hardwiring a CMYK mode into GIMP would be a serious case of under‑design. Why go through all the trouble of introducing that when it cannot deal with a simple poster, printed in black + orange, or the milk carton?
2. control
The second most important thing to understand is that preparing artwork for the printing press means needing total control over the plates. This not only means a flexible plate set‑up as outlined above. It also requires that every bit of experience that a user has with the particular printing press can be used to fine‐tune each plate. I am not underestimating what this is going to take: basically the full GIMP functionality, including any plugin.
3. creative work
The third thing to understand is that creative work is on‑screen work. We must focus on the loop that exists between users, the tools they use and the image that appears as a result, again inspiring the next step of users. If I may be so bold: during creative work the image does not exist on disk, or in RAM, it only exists on the screen.
The natural medium of the screen is RGB pixels. That is why I say: creative work is RGB work.
4. what about CMYK files?
If one receives a file in CMYK format, we know by now that it was destined for the printing press—actually, one particular printing press that is is supposed to be fine‐tuned for. With that knowledge there can be two reasons we are touching it at all:
- it needs further fine‐tuning for that press, best done in CMYK;
- it is a found‐image that goes into a new creative work, for that it needs to be imported and converted to RGB.
5. workflow
The last thing that we have to understand about the activity is how eclectic real‐life workflow is. In theory it is simple: one creates artwork, separates it for the plates, then prints it on the press. That is also the clean model when it comes to color models.
Creative users live a bit more iterative: start creating; set up the separation to see what is possible in the end; fine‐tune that; create some more; fine‐tune some more; get feedback and adapt the creative work with that; get a print proof and do a wholesale overhaul of the separation and fine‐tuning; some last‐minute creation; print it on the press.
It is easy to see that the rigid theoretical workflow does not support creative real‐life. The rigid workflow is the the norm in software today and it inhibits creative users to work as freely as they can imagine.
form‑fit
Now that we fully understand the activity, we can work on squaring the circle. Read all about it next time.
Labels: GIMP, GIMP redux, lecture, practical, product phase
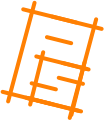
6 comments · post a comment
- at 20 May, 2009 21:23, commented
- Peter, please consider black generation and trapping as critic parts of the workflow too.
In theory, RGB could be translated to CMY, but since inks are not perfect you have to add black. And black has been always the most difficult part of the conversion (GCR and UCR stuff).
When you work for print you have two alternatives: Work with spot colors (1 print pass for each color. Pantone inks, for instance) or convert an RGB image to CMYK or CMYKOG (hexachrome) separations.
Both need control in overprint and trapping, but separations need control in the black generation as well. It's not a minor issue.
There's also a third option, that is mixing CMYK separation with spot colors.
Take an air freshener can, for instance. They use CMYK+spot, and sometimes a photograph of a field of flowers blends with a solid spot color.
I know that it was discussed in the list already, but this first part of your article seems to completely miss this subject. - at 22 May, 2009 00:45, Joe commented
- Seems like a complex subject. I've heard CMYK is the norm for relatively small-time graphic artists getting their work printed, but I could easily be remembering wrong.
From what I understand, one of the big problems with RGB is it represents more colors then CMYK; so when you go to print your an image, you find the colors are slightly off. Seems this could be solved with some sort of color profiling system, that would ensure what you see on your canvas (on screen) is within the gamut of your target format (CMYK or whatever).
That way you'll see exactly what you'll get from the printer, but without having to really store the image in CMYK. It'd also be more flexibly for other plate setups.
Anyway, my 2 cents, heh. - at 22 May, 2009 19:01, commented
- In response to Joe: GIMP has this system, it is called doing a Soft Proof. You can have GIMP display your RGB image as if it was printed. This is done based on a CMYK profile. So if you have the CMYK profile for your specific printer, paper and inks, then GIMP can show you which colors are out of gamut and how the printout will look like. Of course this also requires a good and reasonably well calibrated screen.
- at 02 September, 2009 23:55, commented
- In my view it's critical that you can use cmyk tools on the "projection" ie that the curves and the colour picker feed you accurate cmyk info. Sounds cpu intense to me since it all has to be realtime.
Personally I would never trust the screen as I have yet to experience a perfectly calibrated system. The histograms and spot cmyk values are hard facts that can help calibrate for output.
To get a responsive system that achieves the above with the setup you mention would be great. But I trust the penalty in response time will be felt. - at 28 March, 2012 18:05, Gez commented
- Heh, I sort of changed my mind :)
Some of the stuff I pointed out in my first comment remain valid though.
In the last couple of years I investigated a lot and figured out ways to work with late-binding workflows with free software, having a good deal of success (I moved to a 100% free software pipe for my press work).
My conclussion about it is that GIMP can provide a good intermediate and late binding workflows with some of the modifications you proposed.
Now I agree that early binding (doing separations before creative work) is a bad design choice. GIMP should focus on allowing flexible and complete intermediate and late binding workflows
Print-ready projections out from creative RGB work seem a good way to achieve that.
There are some crucial things to observe thought:
- The projection to substractive models should be a proper color managed conversion using icc and device-link profiles.
- Using spot plates and CMYK primaries is equally important. Spot plates are needed for special inks (the milk carton example) but sometimes having control over primaries to use them as spot plates to tweak the separation is useful as well.
- Black and gray generation from RGB is always a problem. A color managed conversion will create its own generation and even though it's possible to tweak that using device link profiles, sometimes controlling the key plate to get clean black and gray elements is crucial. This is pretty much using K as a spot channel as pointed above, but it's impact on print output is far more important.
- It's arguable that corporate colors should be printed using spot inks, but sometimes specific CMYK values are mandatory. If our client asks for a CMYK file with specific CMYK values for their logo, we're in trouble if we can't deliver.
After thinking about this for a while, I'm sure that projections can cover all of these needs if GIMP allows to create a special type of layers, maybe called "plates", where you can define the type (Spot/CMYK). Making those layers to be "projected" and previewed properly in the final composite and stored as channels in the final file, we'd have all that we need for print. - at 05 February, 2013 15:45, SchaedelDX commented
- We produces newspapers, about 400 000 a day. We use the the cmyk, we have to. And we will not need something else. Even if we want to change the plate production it costs much more than 1 million dollar. Usually we use open source applications on the clients. In this case we have a big problem and have to use Photoshop for professional cmyk editing and producing.
If you like to ask Peter one burning question and talk about it for ten minutes, then check out his available officehours.
What is Peter up to? See his /now page.
- info@mmiworks.net
- +49 (0)30 345 06 197
- imprint